Complete Guide to Shisha Charcoal Production Line: From Raw Material Carbonization to Final Packaging
As global demand for shisha charcoal continues to grow, particularly in the Middle East, Africa, and Europe, many charcoal producers are adopting automated production lines to enhance efficiency, output, and product quality.
This article guides you through the entire shisha charcoal production line, from raw material preparation to final packaging, utilizing professional machines designed specifically for this purpose.
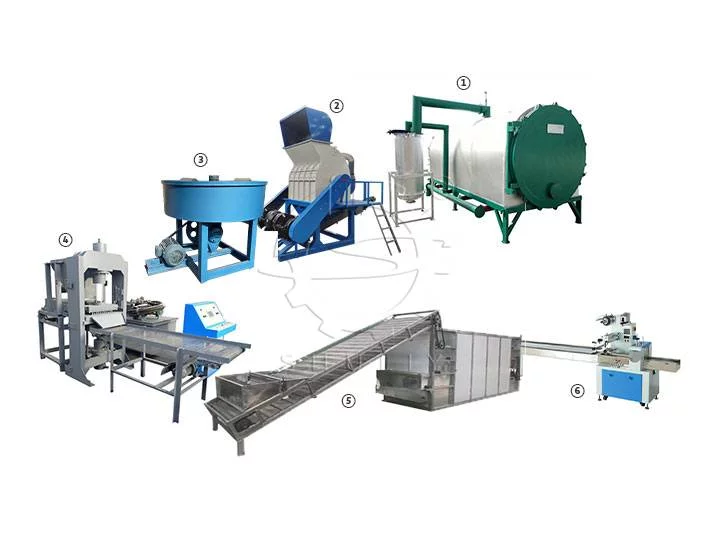
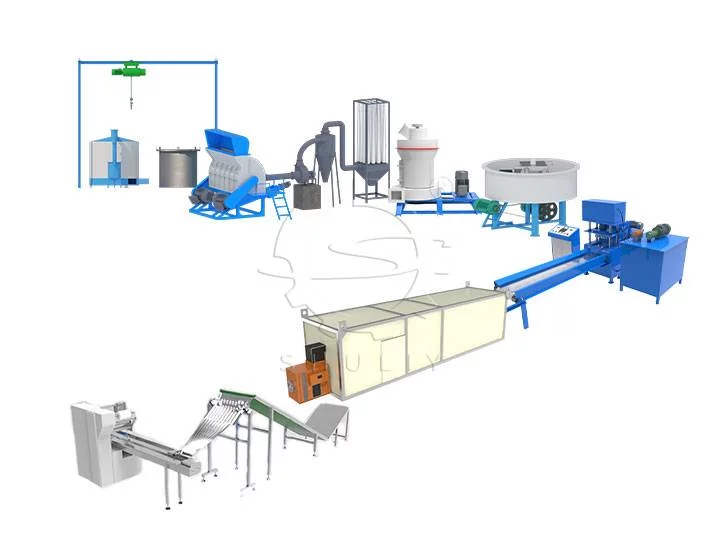
Step-by-Step Shisha Charcoal Production Process
Raw material carbonization: carbonization furnace
The production begins with carbonizing raw biomass materials such as coconut shells, fruitwood, or sawdust in a carbonization furnace. This process removes moisture and volatile components, converting the material into high-carbon charcoal suitable for briquetting.
Advantages:
- High carbon content
- Low ash residue
- Clean and smokeless base charcoal
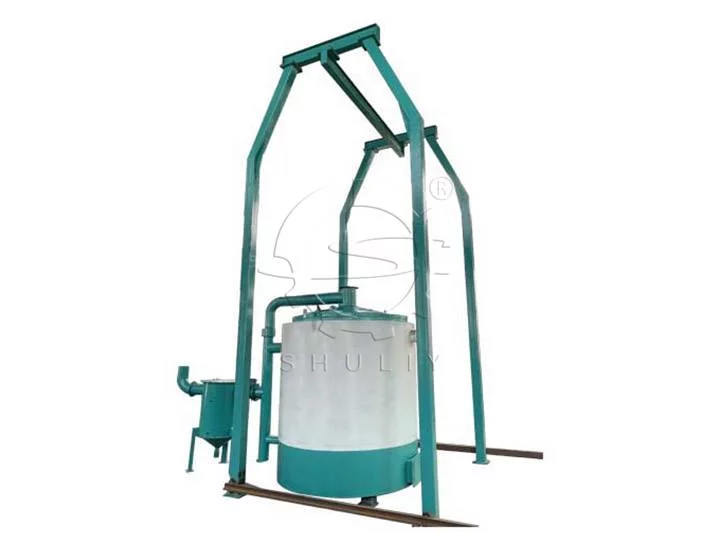
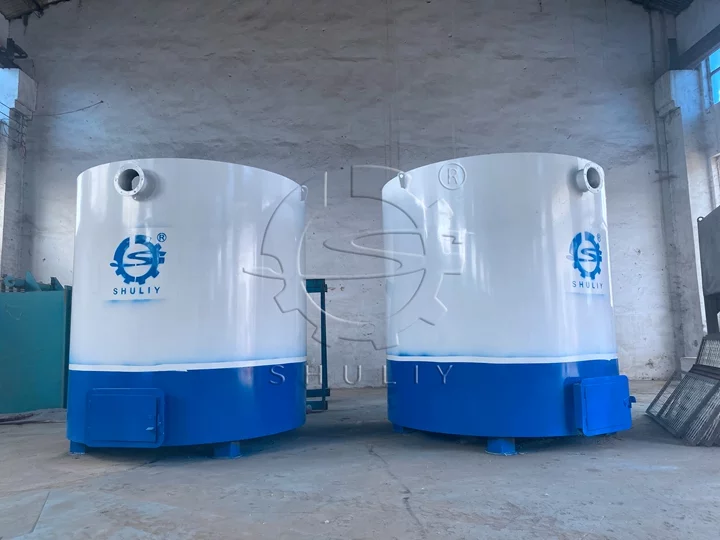
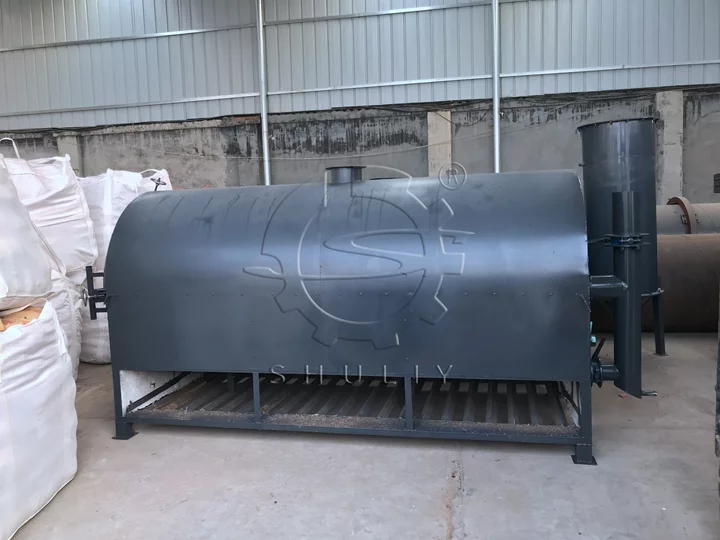
Charcoal crushing: charcoal crusher
Once carbonized, the bulk charcoal needs to be crushed into fine powder. A hammer mill or wheel grinder is typically used to ensure the charcoal reaches a uniform, fine consistency for pressing.
Why it matters:
- Ensures tight bonding
- Improves briquette strength and density
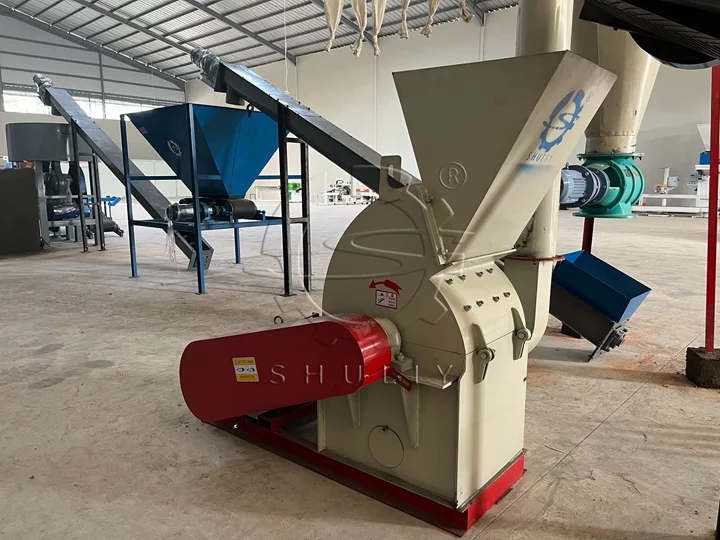
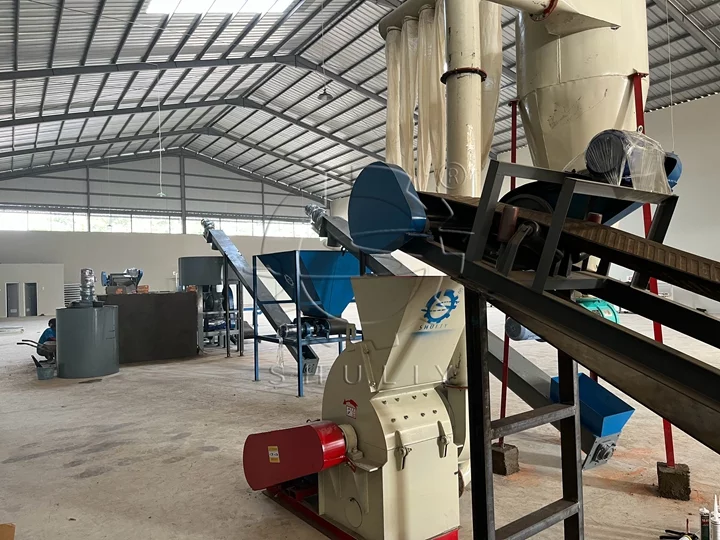
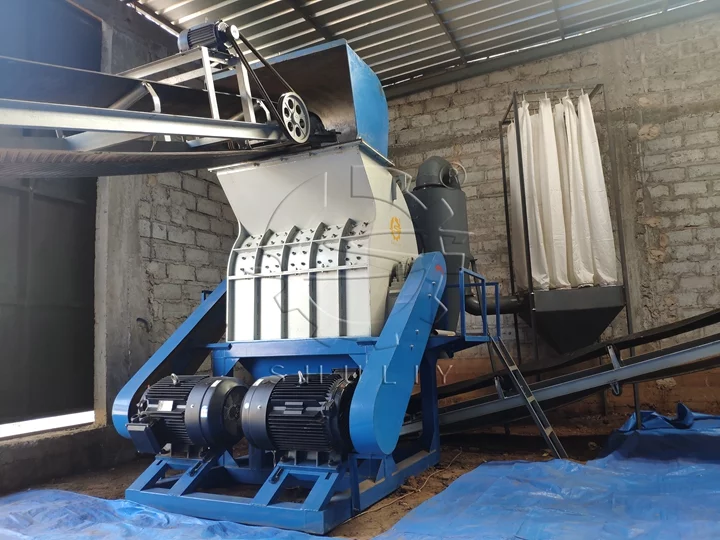
Binder mixing: charcoal mixer
The fine charcoal powder is mixed with a natural binder such as starch and a small amount of water. A horizontal mixer ensures the uniform blending of all ingredients, which is critical for achieving solid and durable briquettes.
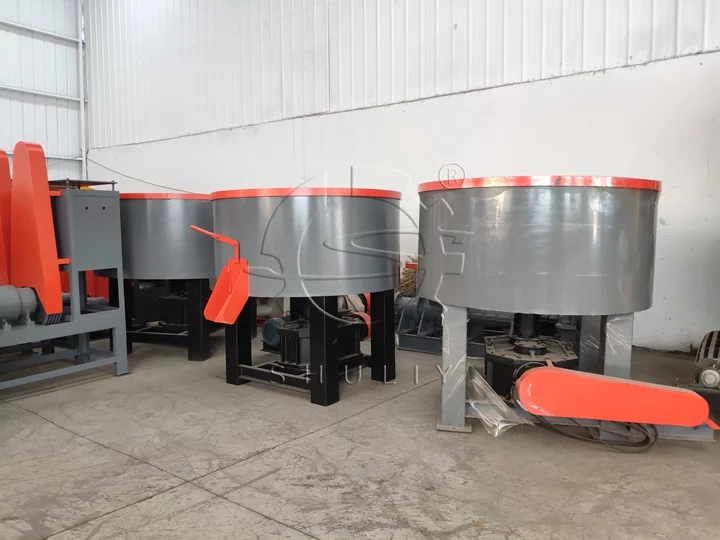
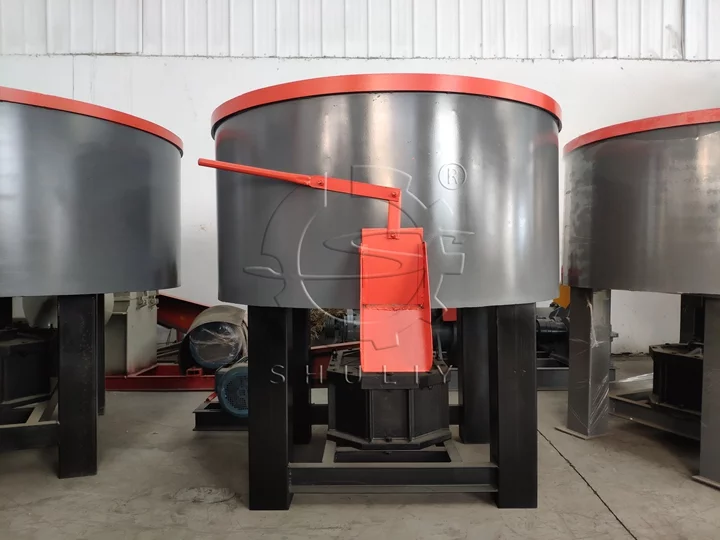
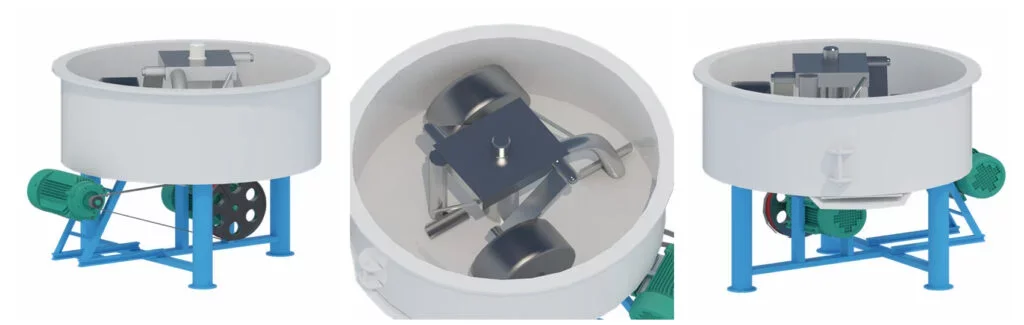
Shisha charcoal briquetting: shisha charcoal press machine
This is the core step of the production line. Depending on market demand, the mixer material is shaped into cubes, hexagons, or round tablets using a high-pressure press machine.
Options include:
- Hydraulic shisha charcoal press
- Rotary tablet press
- Cubic briquette press
Features:
- Customizable shapes and sizes
- Consistent weight and density
- High output, low breakage rate
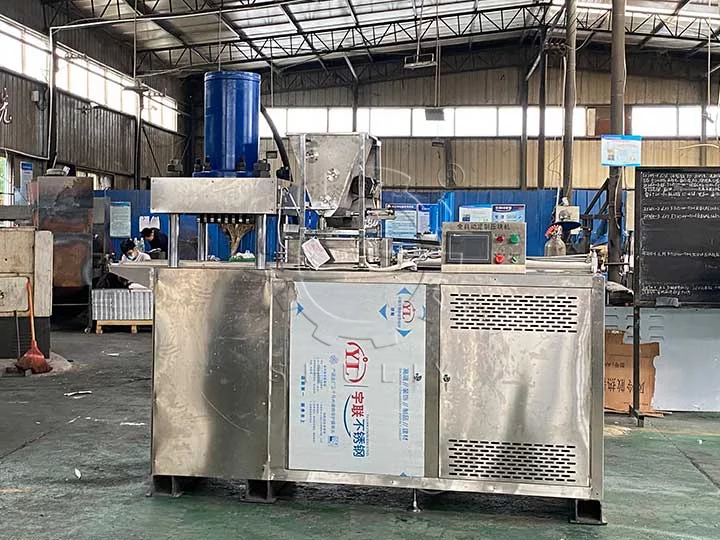
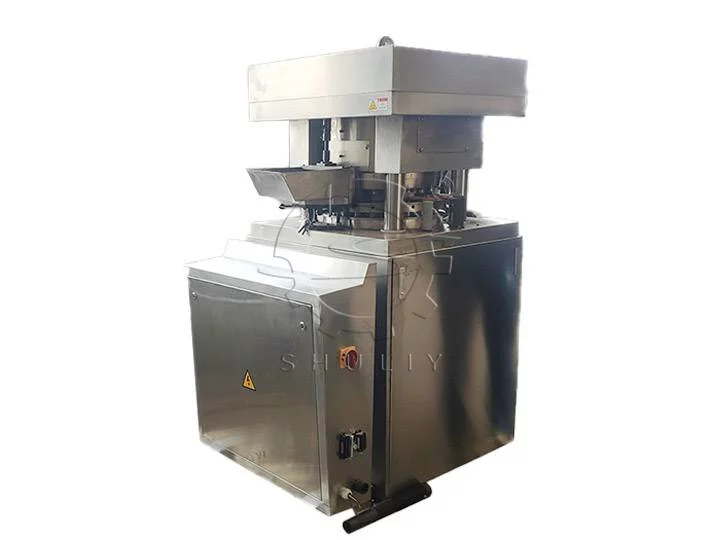
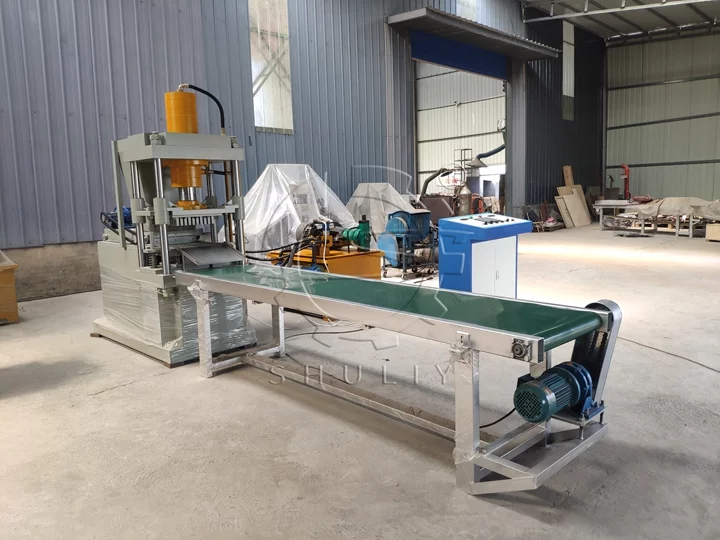
Charcoal drying: drying oven or continuous dryer
Freshly pressed charcoal is still moist and must be thoroughly dried. A drying oven ensures even drying of briquettes without breaking or cracking.
Benefits:
- Prevents mold
- Increases shelf life
- Prepares charcoal for packaging
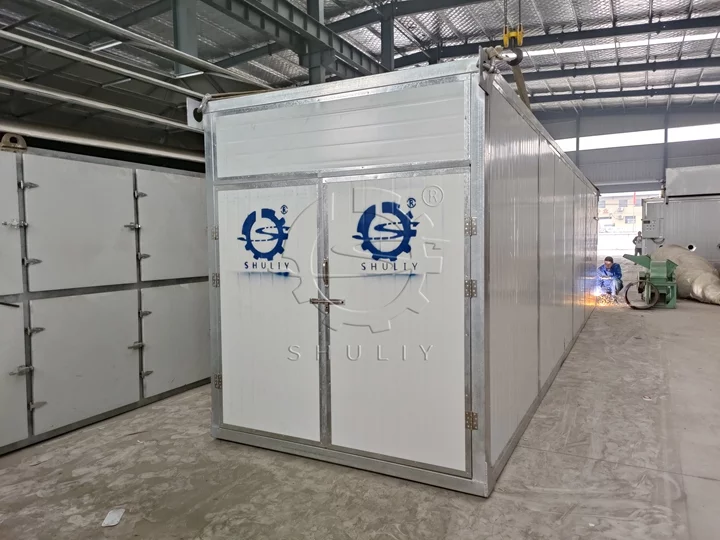
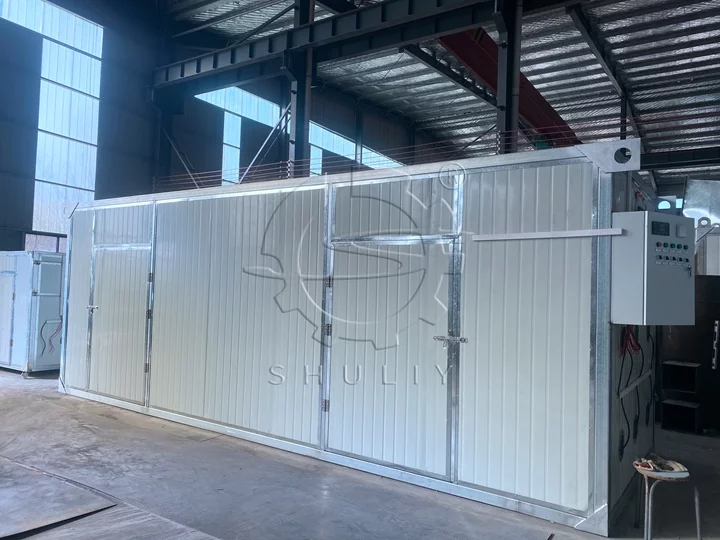

Final packaging: hookah charcoal packaging machine
Finally, the dried charcoal briquettes are packed into plastic bags, boxes, or cartons using a pillow packing machine, which can keep the product dry and dust-free.
Key Features:
- Accurate weighing
- Fast packaging speed
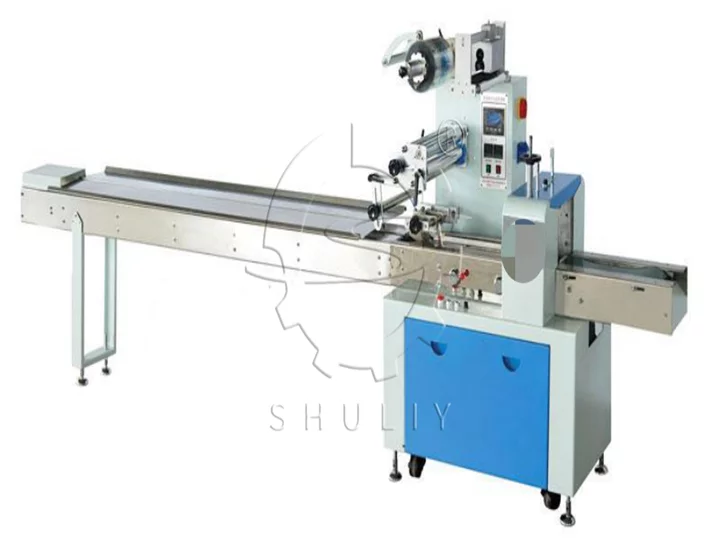
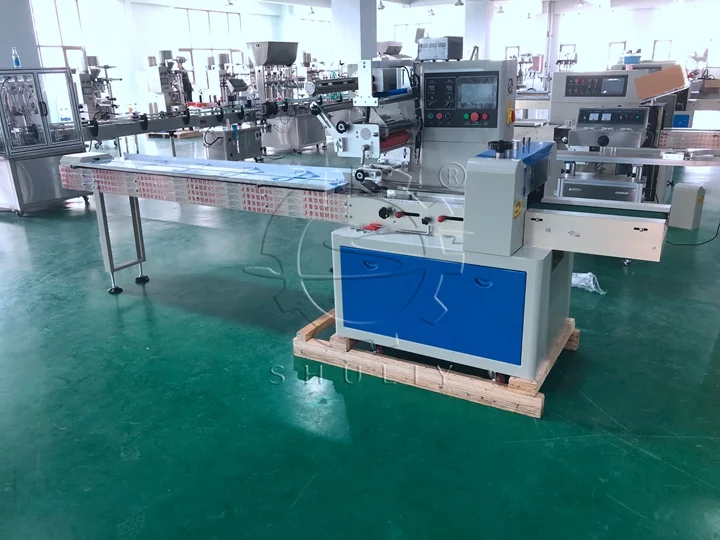
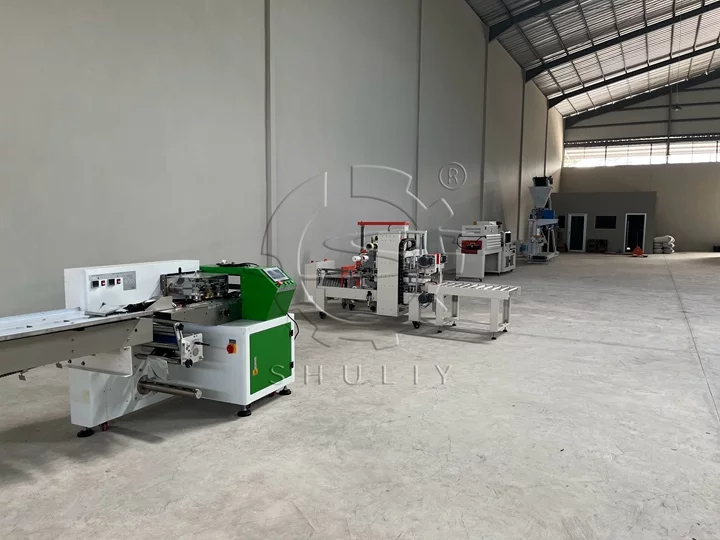
Conclusion
From carbonization to final packaging, the modern shisha charcoal production line enables producers to manufacture consistent, high-quality products at scale.
Whether you are starting a new charcoal business or upgrading from manual production, investing in a complete shisha charcoal machine line will significantly improve your efficiency, product quality, and market competitiveness.
If you want to get the detailed parameters, quotation, and video of the whole production line, please contact us.