The Importance of Charcoal in the Metal Smelting Industry
In today’s increasingly stringent global carbon emissions, the metal smelting industry, as a traditional high-pollution, high-energy-consumption industry, is facing the double pressure of technological innovation and green transformation.
In this context, charcoal, as a clean and renewable carbon-based reductant, is gradually favored by metallurgical enterprises. And it shows a broad application prospect in the smelting process of ferroalloys, non-ferrous metals, and so on.
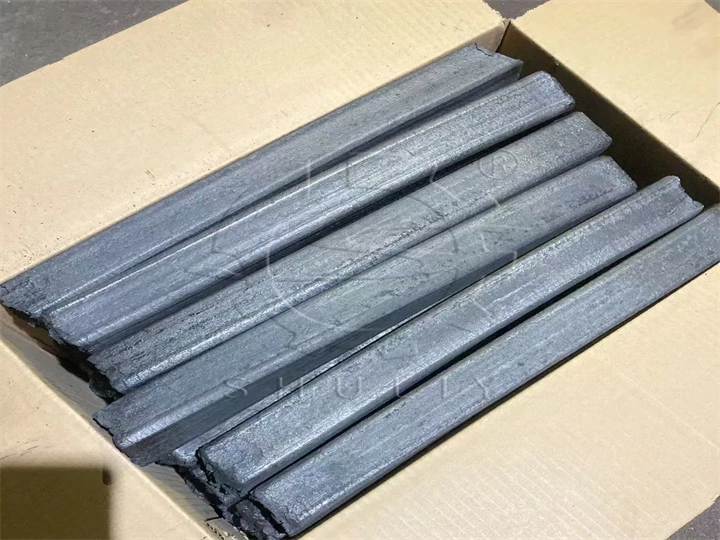
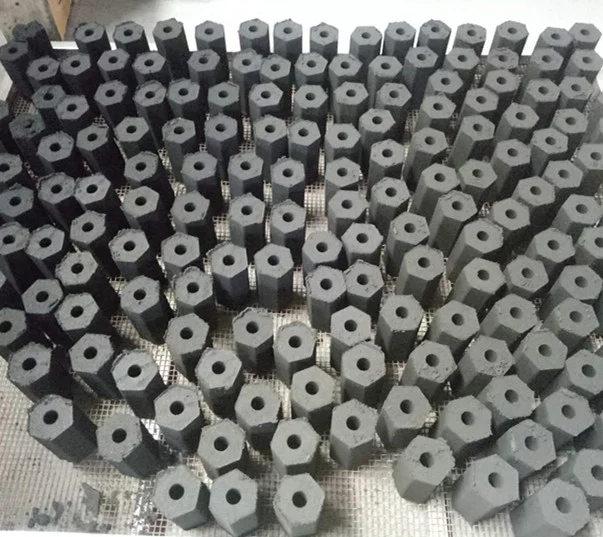
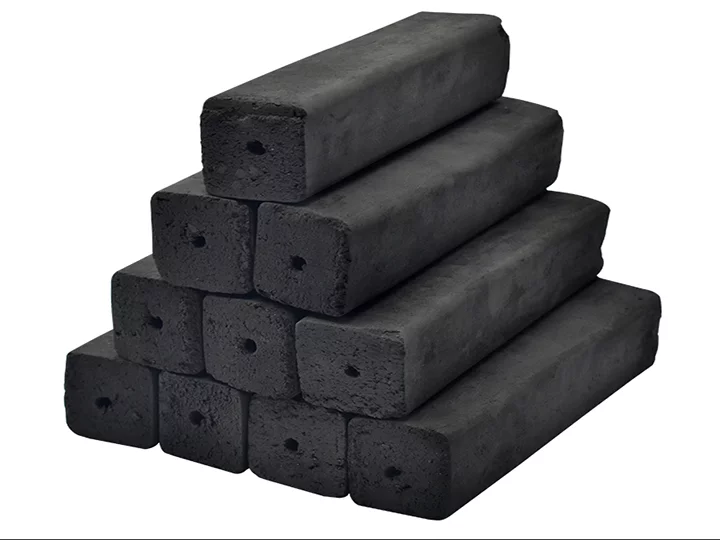
Limitations of traditional reductants
Conventional metal smelting relies heavily on coal and coke as reducing agents to reduce metal oxides to pure metals. However, there are several major problems associated with the use of these fossil fuels:
Serious pollution: combustion releases a large amount of SO₂, NOx, and other harmful gases, leading to acid rain, haze, and other environmental problems.
High carbon emissions: the coal-based smelting process is one of the main sources of greenhouse gas emissions.
Non-renewable resources: coal resources are depleted year by year, with sharp price fluctuations and unstable supply.
High ash content and impurities: affecting the quality of smelting products and reducing output efficiency.
These problems have prompted the metallurgical industry to accelerate the search for new reductants that are more environmentally friendly and stable.
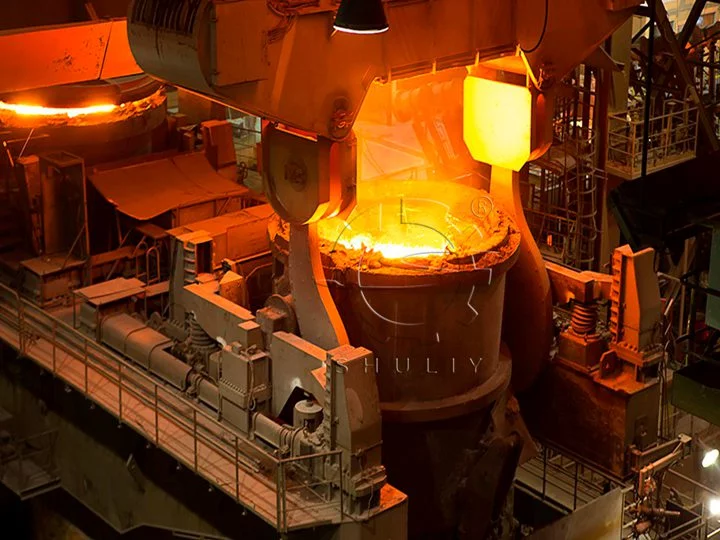
Why is charcoal suitable for use as a metallurgical reducing agent?
Charcoal, as a carbonaceous material made from plant-based raw materials and high-temperature oxygen-free carbonization, has unique physical and chemical advantages. It is particularly suitable for use as a substitute for some traditional reducing agents:
High carbon, low ash: over 75% carbon content with minimal ash and sulfur—improves smelting quality.
Easy to ignite, high heat: burns steadily at high temperatures, ideal for smelting.
Renewable and carbon-neutral: made from biomass, supports eco-friendly production.
Low impurities: clean fuel with minimal slag or metal contamination.
Versatile forms: can be processed into powder, lumps, or briquettes for various uses.
Therefore, charcoal is not only an ideal choice for energy saving and emission reduction in the metallurgical industry but also an important carrier for upgrading to green manufacturing.
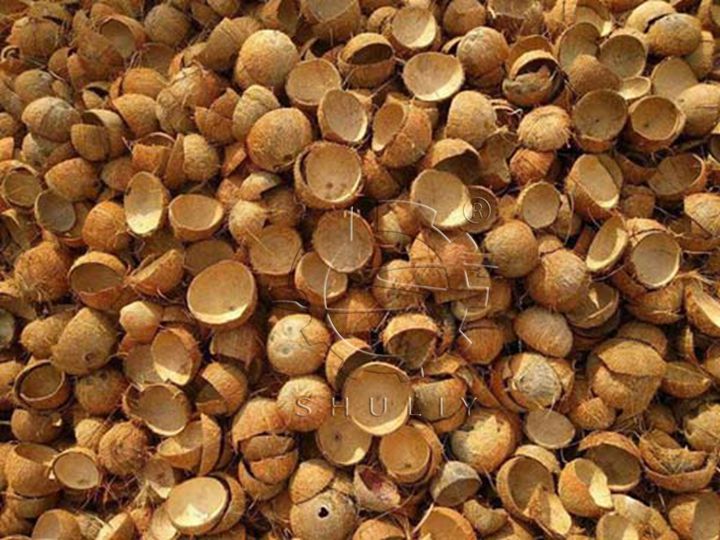
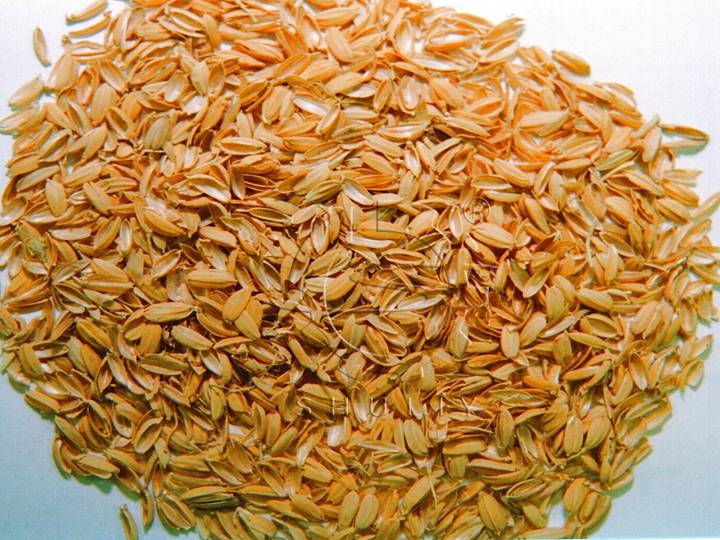
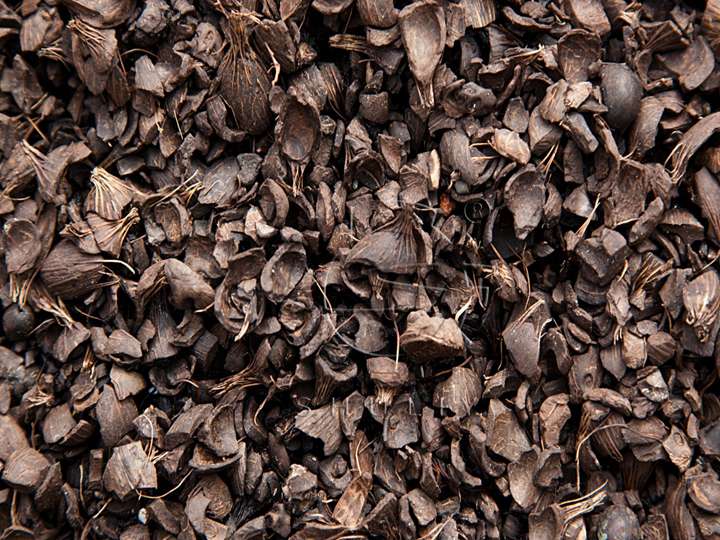
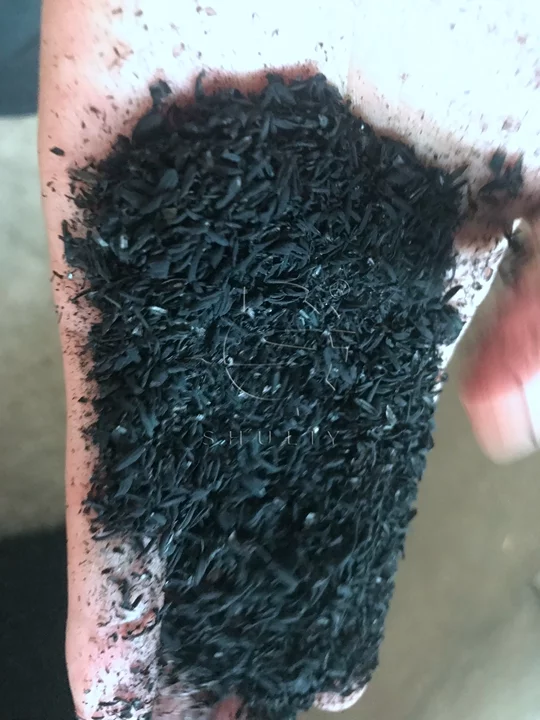
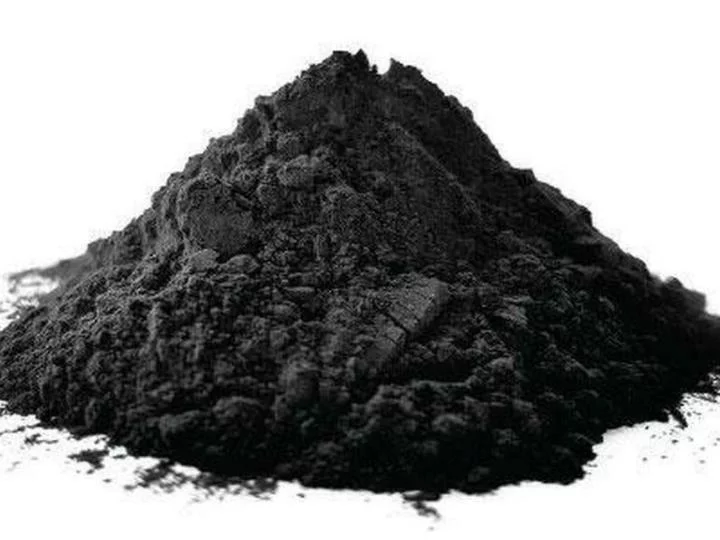
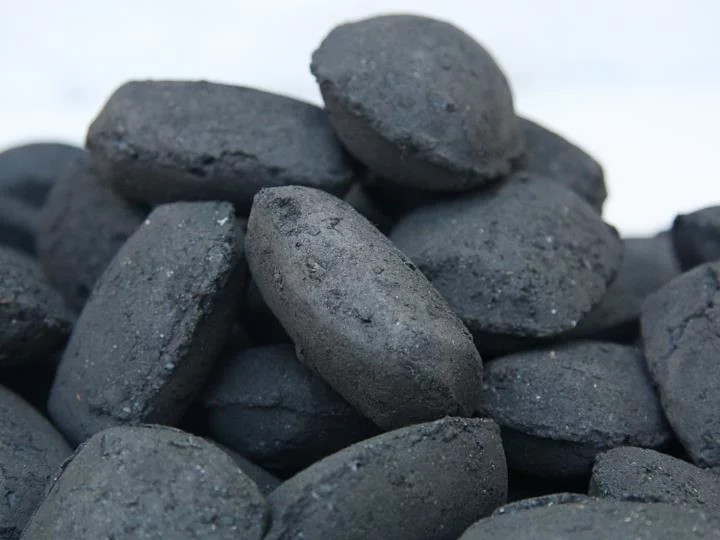
Shuliy charcoal production line: stable charcoal supply for the smelting industry
Shuliy Machinery specializes in environmentally friendly charcoal equipment solutions and has built a mature and efficient charcoal production line for the large-scale charcoal needs of the metallurgical industry, including:
Carbonization furnace: turns wood, shells, or bamboo into high-quality charcoal through high-temperature carbonisation.
Carbon powder machine: crushes charcoal into fine, uniform powder for briquetting.
Charcoal mixer: evenly blends charcoal powder with binder to enhance briquette strength.
Charcoal briquette machine: compresses charcoal powder into solid blocks for industrial smelting.
Drying room: dries briquettes to improve hardness and storage stability.
The whole production line supports customization according to output, stable operation, energy saving, and environmental protection. It is widely used in all kinds of metal smelters and charcoal products export enterprises.
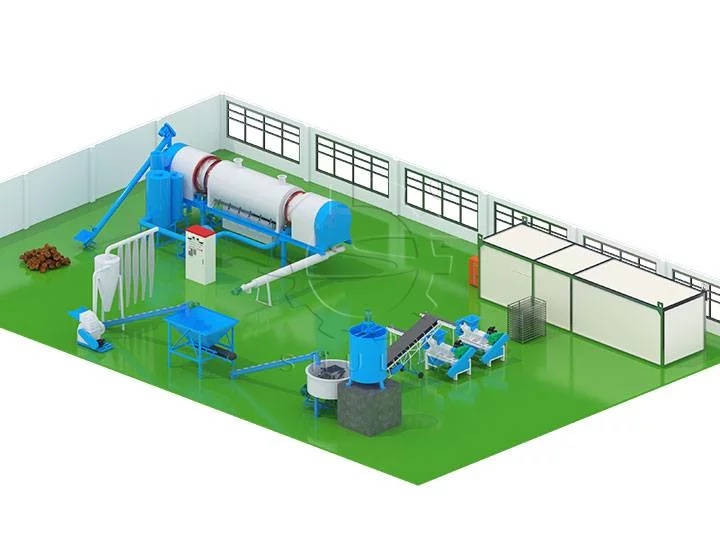
Contact us for customized charcoal solutions!
As the shift toward green smelting accelerates, charcoal is becoming a cleaner, more sustainable alternative to traditional reducing agents. At Shuliy, we’re proud to support this transformation by offering reliable charcoal production equipment and tailored solutions for the metallurgical industry.
If you’re looking to reduce costs, improve product quality, and meet carbon emission goals, we’re here to help.
Contact us today to get detailed equipment specifications, competitive pricing, demo videos, and sample testing support.
Let’s work together to shape a cleaner, low-carbon future in metal smelting.